This week we address the Use of Face Coverings which is now mandatory if you live within metropolitan Melbourne or Mitchell Shire.

Key Points
- You must wear a face covering whenever you leave your home, unless an exception applies, this includes at your place of work. A face covering needs to cover both your nose and mouth. It could be a face mask or shield.
- If you live in other parts of Victoria it is recommended you wear a face covering when you leave home and are in situations where it is difficult to maintain physical distance of 1.5 metres between yourself and others.
- A face mask includes any paper or textile covering designed or made to be worn over the nose and mouth to protect the wearer. It does not have to be medical grade and you can make your own.
- Infants and children under the age of 12 are not required to wear a face covering. Due to risk of choking it is not safe to use a mask on child under two years of age.
- A fine of $200 may be issued to people who do not wear a face covering and do not have a valid reason for exception.
- The best way to protect other people against coronavirus (COVID-19) is staying home when you feel unwell, keeping 1.5 metres apart, wash your hands often, and cough or sneeze into your elbow or tissue. Face coverings add an additional protective physical barrier to protect you and your loved ones.
To learn how to make your own cloth mask visit the following link:
Reusable & Disposable Masks
Disposable P2, N95 or surgical masks can be used and must be disposed of responsibly in the rubbish bin after one use.
A cloth face covering can be washed and re-used. It should be washed after each time you use it and before you put it back on. It is a good idea to have at least two, so you always have a clean one available.
Keep a paper bag or zip lock bag with you to carry fresh face coverings to keep them clean.
When Do I Have to Wear a Face Covering?
Unless an exception applies, if you live in metropolitan Melbourne or Mitchell Shire you must wear a face covering when you leave your home for one of the four reasons: shopping for food and supplies, recreation or exercise, medical care and caregiving, and study or work – if you can’t do it from home. This includes travelling on public transport or in a car with people outside your household.
If you live in metropolitan Melbourne or Mitchell Shire and must travel outside of these areas, for necessary goods and services, medical care and caregiving, or study or work, you must continue to wear a face covering.
Similarly, if you live outside metropolitan Melbourne or Mitchell Shire and must travel inside these areas, for necessary goods and services, medical care and caregiving, or study or work, you must wear a face covering.
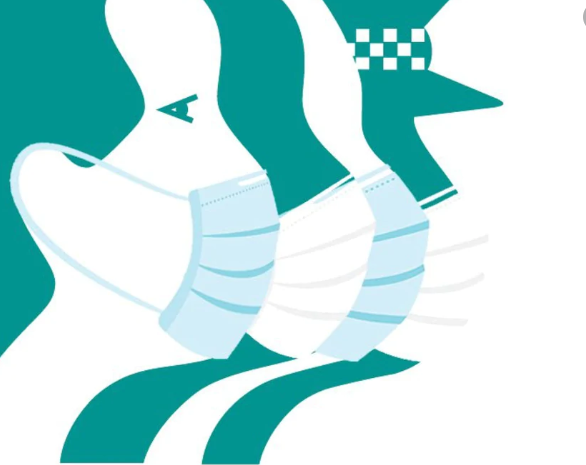
Lawful Exceptions for Not Wearing a Face Covering
A face covering is not required in the following circumstances:
- Infants and children under the age of 12 years.
- A person who is affected by a relevant medical condition – including problems with their breathing, a serious skin condition on the face, a disability or a mental health condition. This also includes persons who are communicating with a person who is hearing impaired, where the ability to see the mouth is essential for communication.
- Persons for whom wearing a face covering would create a risk to that person’s health and safety related to their work, as determined through OH&S guidelines.
- Persons whose professions require clear enunciation or visibility of their mouth. This includes teaching or live broadcasting.
- When the individual is doing any exercise or physical activity where they are out of breath or puffing; examples include jogging or running but not walking. You must have a face covering on you and wear it when you finish exercising.
- When directed by police to remove the face covering to ascertain identity.
- The person is travelling in a vehicle by themselves or with other members of their household.
- When consuming food, drink, medication or when smoking/vaping.
- When asked to remove a face covering to ascertain identity, for example at a bank branch or bottle shop.
- When undergoing dental treatment or other medical care to the extent that the procedure requires that no face covering may be worn.
- During emergencies.
You must carry a face covering with you when leaving home for one of the four reasons, even if you don’t need to wear it while undertaking your current activity, for example you can take your face covering off to eat. If you have a medical condition that prevents you from wearing a face covering at all times you don’t need to carry it with you.
How to Put on a Mask
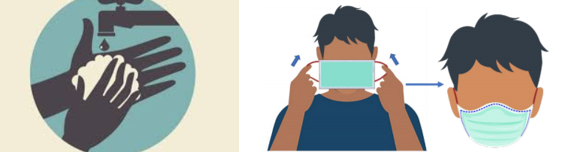
- Clean your hands thoroughly with soap and water (minimum of 20 seconds) or hand sanitiser before touching the mask or removing it from its packaging. Dry your hands and make sure you do not touch any surfaces before you get your mask.
- Remove a mask from its packaging and make sure the mask has no obvious tears, holes or faults. Avoid touching the front of the mask.
- Identify the top of the mask (generally it has a stiff bendable edge that will mould to the shape of your nose) and the front of the mask (normally a mask is coloured on the front) with the white side towards your face.
- If your mask has ear loops, hold the mask by the ear loops and place a loop around each ear. If your mask has ties bring the mask to nose level and place the ties over the crown of your head and tie with a bow (leave the bottom set of ties at this time).
- If your mask has a band, hold the mask in your hands with the nose piece or top of the mask at your fingertips, the headbands will hang loosely below your hands, then bring the mask to your nose level and pull the top strap over your head to rest on the crown of your head, then pull the bottom strap all the way over your head to rest at the nape of your neck.
- Pinch the stiff nose piece to the shape of your nose.
- If your face mask has ties take the bottom ties (one in each hand) and tie at the nape of your neck with a bow.
- Adjust the bottom of the mask over your mouth and under your chin.
Whilst Working, Can I Have Breaks?
It is important that you wear your face covering when at work, but some people may require short breaks from wearing their face covering. When you do so, ensure you are not near other people, and follow this advice when removing your face covering:
- Wash your hands for at least 20 seconds with soap and water or use alcohol-based hand sanitiser containing at least 60% alcohol.
- Don’t touch the front of the mask or your face.
- Carefully remove your mask by grasping the ear loops or untying the ties. For masks with a pair of ties, unfasten the bottom one first, then the top one.
- If your mask has filters, remove them and throw them away. Fold the mask and put it directly into the laundry or into a disposable or washable bag for laundering. Disposable masks should be disposed of responsibly.
- Clean your hands again.
Only a short break should be required.
Wearing a Mask
How do I stop face covering fogging up my glasses?
Make sure the face covering is fitted and pinched on your nose if possible. Put your glasses on after the face covering. Wash your glasses with detergent and water to create a film to prevent fogging. You can also use micropore tape (available at all pharmacies) to tape the face covering along the bridge of your nose and cheeks, then put your glasses on top. Or put a folded tissue across the bridge of your nose, then put your face covering on and your glasses on top.
Do I need to wear a face covering when I am driving?
If you are driving alone or only travelling with people from your household, you do not need to wear a face covering. You should put your face covering on before you leave your vehicle or if you wind down the window to talk to someone.
If you are driving with people for work or people you don’t live with then you must wear a face covering.
You must wear a face covering if you are a passenger or driver in a commercial vehicle such as a taxi or uber.
Do I need to wear a face covering at my place of work or my desk even if I am 1.5 metres away from others?
Yes, if you live in metropolitan Melbourne or Mitchell Shire you must wear a face covering when you leave your home for one of the four reasons, which includes working, unless an exception applies. If you work in an enclosed office on your own, you don’t have to wear a mask while at your desk. If someone enters your space and when you leave it, you need to wear a mask.